Precision optical imaging systems span a wide variety of markets and applications including semiconductor, life science, medical device, aerospace, defense, and other industries. Often these imaging systems necessitate demanding performance requirements including diffraction-limited wavefront image quality, pixel or sub-pixel image distortion, as well as broad-band chromatic aberration correction. In order for the optical system to be manufactured to these requirements, the design often requires various advanced compensation methods during the build process including the use of melt compensation.
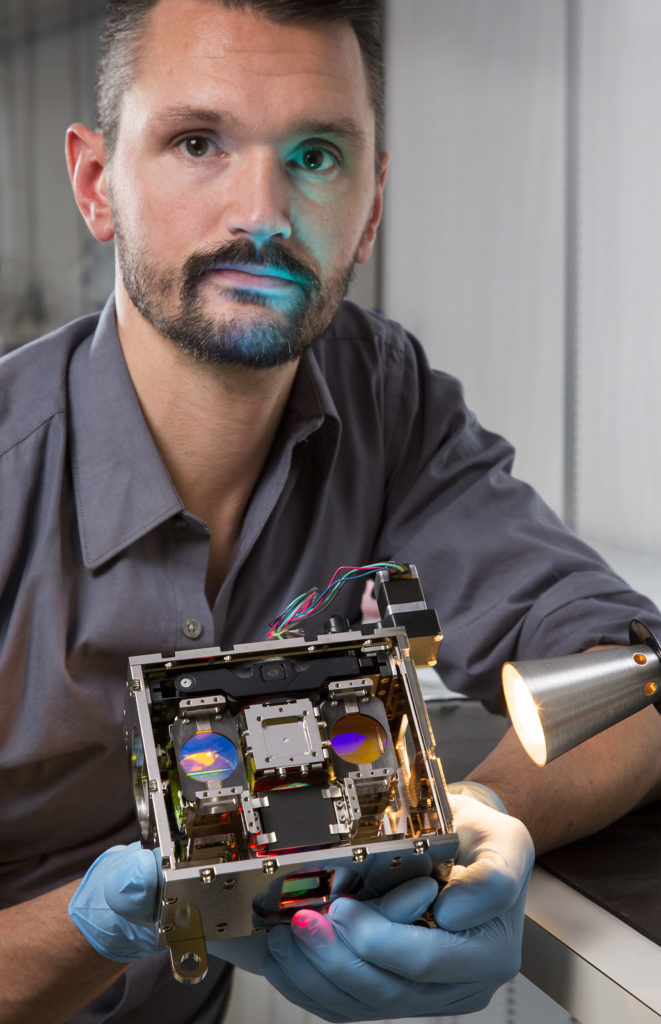
One technique for melt compensation prescribes element-to-element airspace values for each serial number assembly. This is a multi-step design process. First, measured index of refraction values from glass manufacturers are fit using glass dispersion formulae and interpolated at the design wavelengths of the optical system. Second, the optical design nominal airspace values are re-optimized in the design software to correct for the measured dispersion of the optical glass. Finally, the optimized airspaces are prescribed to the manufacturing and assembly team.
Another option one may consider with respect to melt compensation is the use of radii as compensators. With this method, one also obtains index of refraction values from glass manufacturers, utilizes glass dispersion formulae, and interpolates at the design wavelengths. Next, the optical design is re-optimized with radii as variables to correct for the as-measured dispersion of the optical glass. Subsequently, optical prints are revised and optical elements are fabricated. Radius melt compensation has several advantages and drawbacks.
Disadvantages:
- Availability and quantities of the raw material for their specific optical design
- Customer delivery schedules
- Potential changes to the opto-mechanical design
- Mixing glass melts may violate the assumptions in your tolerance model
Advantages:
- Improved as-built performance
- Potentially less system-to-system variability
- Increased performance margin for other optical tolerances such as alignment errors
For many optical systems and their performance requirements, melt compensation is an ideal manufacturing process. However, even if a design is suited for melt compensation, it is not uncommon for a specific combination of glass melts to limit the efficacy of the technique. In this case, the compensated lens performance may not be regained to a satisfactory level. In order to mitigate the risk of unsatisfactory melt combinations, consider modeling the effect of many melt combinations, and make sure to model the complete build process when tolerancing the optical design. You may also consider modeling a sub-set of radii as compensators to minimize documentation changes required for procurement. Of utmost importance to the success of melt compensation is a thorough understanding of your melt metrology and material certificates. This includes the number of index data points, accuracy of refractometry, and wavelength spectrum range of the data, as extrapolated melt fits outside the design spectrum is not recommended.
The engineering and manufacturing teams at Optikos have extensive experience executing melt compensation in order to achieve the most demanding performance requirements for precision imaging systems. This technique is not limited to low volume imaging systems and can be utilized across the entire cost/performance curve. If you need help designing or manufacturing your next optical system, please contact Optikos to see how we can help move you forward.