Primary Challenges & Breakthroughs
- Augmented reality (AR) lens manufacturing faces important testing challenges due to complex multi-parameter validation requirements and sequential testing dependencies.
- Cycle time constraints create critical bottlenecks for augmented reality optics, with comprehensive performance testing of high-precision AR lenses averaging 3-8 minutes per unit—directly impacting manufacturing throughput, workforce costs, and delivery schedules.
- A new Optikos LensCheck™ and advanced robotics strategy has achieved 50% reduction in cycle time while delivering substantial throughput gains during peak production cycles for a Fortune-500 client.
Overview
The world of lens manufacturing is ruled by three important production parameters: quality, investment, and time. Within this matrix, the testing phase of optical systems is paramount because of the “zero-tolerance for defects” nature of the sector. What garners criticality around this phase of the manufacturing process is the rapid growth of advanced infrastructure demands and emerging technologies, most of these relying on high-performing optical components. Optikos® has been championing optical testing for over four decades through our extensive metrology and IQ Lab™ services, making sure the solutions that pass through our hands operate reliably, efficiently, and sometimes, even above expectations.
An important indicator that is impacted by the performance testing of optical systems is cycle time. This metric helps in matching production capability with order demands, and thus, directly influences business realities from production planning and capacity management to bottleneck identification and resource allocation.
Optikos experts have been analyzing the average cycle time linked to internal projects, as well as the available data from other industry resources, and were provided with the opportunity to test a newly developed automation strategy with a Fortune-500 client on their upcoming augmented reality (AR) system program. This strategy was aimed at enhancing repeatability and delivery speed for optical testing, as well as significantly reducing error rates during quality checks.
About The Client
Our client is a multinational technology corporation specializing in software development and advanced technology integration, with a growing portfolio of solutions supporting defense modernization and next-generation technology systems.
The Project
Optikos developed an automated optical testing solution that would enable the high-volume manufacturing of next-generation AR lens assemblies and meet our production schedule. Project deliverables included an operational testing system for an immediate need to test over 20,000 optical systems in a six-month timeline while preparing to scale up to 80,000 tested units per year.
The Challenge
This high-volume lens assembly project required a reliable, scalable, and cost-efficient testing solution that could handle increasing production volumes and would not affect manufacture profitability for the client.
The testing process for each lens included measuring focal length and Modulation Transfer Function (MTF) both on- and off-axis. This is because AR systems have much wider fields of view than other traditional optics, and users expect consistent image quality whether they are looking at the center or edges of the display. Initially, the operation took approximately six minutes per lens on a single LensCheck™ system which is the Optikos quality control solution for optical system production and prototyping. After calculating the cycle time affiliated with this operation, the team concluded that the testing status quo would not be compatible in the long term with the project requirements of the client.
A second process iteration meant deploying two LensCheck units in parallel, which increased throughput to three minutes per lens. However, even with two LensChecks and a reduction in cycle time, the cost threshold grew by utilizing more technicians to operate the equipment. This became the next major hurdle to solve. The bottleneck posed a risk to production efficiency, labor costs, and schedule commitments, particularly with the client forecasting a production of 80,000 lenses per year.
To comfortably accommodate the manufacturing demands, Optikos needed to develop an automated solution that combined the use of the two LensCheck systems with a collaborative robot. Our team of engineers created an internal software program to allow the robot to seamlessly interface with our LensCheck systems by sorting tested lenses into “pass” and “fail” bins, and reloading the LensCheck when the test was done. By incorporating a barcode scanner, Optikos was able to achieve full traceability of test results to lens serial numbers. This step helped improve batch-to-batch consistency and overall finished product quality.
The goal of the automation was to enable the unattended testing of one hundred lens trays, reducing the initial test time per lens by three minutes while simultaneously increasing daily throughput by up to 50% during peak production periods.
The Optikos Way At Work
Optikos developed a custom automated testing solution, shown in Figure 1, by integrating its in-house LensCheck systems with a Universal Robot UR5e robotic arm. AR lenses are typically lightweight, making the UR5e appropriately sized without being over-engineered for the application. The system was programmed to autonomously test trays of one hundred lenses, eliminating the need for a technician to handle each unit individually.
Some of our key project developments include:
- Software and mechanical engineering investments that allowed the robot to interact with a tray of lenses under test, barcode scanners, and the LensChecks.
- Creating a robotic handling system that could manage high-volume test cycles without operator intervention.
- A cap-ex investment of approximately $210,000 for development, robot acquisition, and integration.
The automated system reduced operator input to simply loading a tray of lenses and pressing the start button within the OpTest software platform. The robot then cycled through one hundred lenses in approximately 300 minutes, enabling consistent and unattended operations across shifts.
Additionally, the automated metrology function facilitated Statistical Quality Control (SQC) which goes far beyond simple pass/fail decisions on product batches. Automated systems capture detailed measurement data for every lens such as exact focal lengths, MTF curves at multiple field positions, transmission values, etc. This rich dataset enables more sophisticated analyses and real-time responses. That is how our quality team could quickly review data to ensure we could identify and eliminate defects or variations in production processes, ultimately enhancing the overall product quality in a timely manner.
Collaboration Style
The program success of our client throughout this project was driven by a collaborative ecosystem of specialized technology partners supporting optical design, precision manufacturing, system integration, and rigorous metrology validation. This collaborative model enabled rapid iteration, system-level optimization, and scalability for full-rate production while meeting demanding technical specifications required for deployment readiness.
Our Results
In retrospect, Optikos managed to implement various process changes between our transition to production build and our mass production phase, measures that have positively impacted the overall quality standard for the final optical product. The automated LensCheck testing solution was one of those changes, which delivered transformational improvements in cycle time, slashing per-unit testing by three minutes. This resulted in:
- A 50% increase in throughput during peak production (averaging a delivery of one hundred additional lenses per day).
- An estimated $712,000 in annual labor savings based on the previous labor rate.
- A payback period of less than four months.
- Improved production scalability and reduced operator dependency for the full production project.
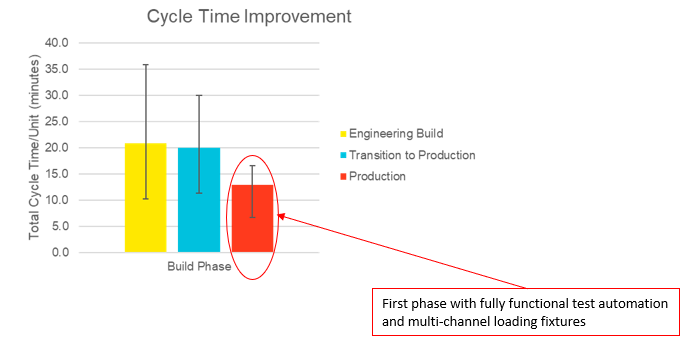
Cycle Time Improvement
This bar chart indicates the total cycle time required to test one hundred AR lenses through an automated system across three different build phases, with error bars representing the range from minimum to maximum cycle times.
The data shows a clear progression toward faster, more consistent lens testing as the automation system is implemented. The cycle time improves by at least 38% and up to 50% from engineering build to production, while variability decreases significantly. The shrinking error bars indicate increasing process control and reliability, which are key production factors impacted by our strategic use of automation.
Automation is king in today’s precision optical testing. Optikos enabled its client to scale manufacturing with confidence, reduce operational costs, and maintain exceptional optical quality standards through a custom-built, cost-efficient testing strategy. This successful AR lens project exemplifies how intelligent test automation and in-house optical expertise can unlock substantial ROI in volume optics production, making way for our client to focus on their product launch, marketability, and innovation.